Frequently Asked Questions
1  Porzellan in der Spülmaschine
Wenn die Geschirrspülmaschine vibrationsfrei läuft und das Porzellan sinnvoll eingeordnet ist, besteht bei den gängigen Spülmaschinentypen keine Gefahr des Bruchs durch zu hohen Wasserdruck mehr.
Der Reinigungsvorgang in der Spülmaschine muß durch Zusatz von Spülmitteln sowie mittels hoher Wassertemperatur intensiviert werden. Die chemischen Zusätze müssen so beschaffen sein, dass sie auch in einer mechanisch ungünstig arbeitenden Maschine und mit hartem Wasser noch einen verhältnismäßig günstigen Reinigungsgrad erzielen. Oft wird dies durch eine Erhöhung der Alkalität erreicht. Spülmittel mit hohem Alkaligehalt sind jedoch nicht nur schädlich für Dekore, sondern ebenso für Glas.
Hohe Spültemperaturen (über 60°C) aber verstärken nicht nur die schädigende Wirkung sondern können auch festhaftende Niederschläge auf dem Spülgut begünstigen. Für die Langlebigkeit des Porzellans bei Gebrauch einer Spülmaschine spielt die Art der Dekore eine wesentliche Rolle. Unterglasurdekore oder solche, die bei sehr hohen Temperaturen in die Glasur eingebrannt werden, sind äußerst beständig gegenüber allen chemischen und mechanischen Einflüssen.
Die Mehrzahl der Dekore wird bei Temperaturen von 1220 - 1250 °C geschmolzen, die hierbei verwendeten Farben sind säurebeständig und geben kein Blei ab. Die Porzellanfarben wurden auch hinsichtlich ihrer Widerstandsfähigkeit gegenüber chemischen Spülmitteln weiterentwickelt.
Ein Optimum an Beständigkeit bei diesem gegensätzlichen chemischen Einwirkungen wie sie einerseits die Säure und andererseits die Lauge darstellen, lässt sich jedoch nur in gewissen Grenzen erreichen.
Trotzdem kann festgestellt werden, dass heute fast alle gebräuchlichen Porzellandekore eine zufriedenstellende Widerstandskraft gegenüber den meisten chemischen Spülmitteln aufweisen.
Ganz sicher hat die langjährige Erfahrung mit Geschirrspülmaschinen gezeigt, dass z.B. Temperaturschocks (d.h. plötzlicher Wechsel von heißem und kaltem Wasser) für Dekore wie auch für Gläser schädlich sind. Die neuen Spülgeräte haben diese Erfahrung bereits bei der Konstruktion berücksichtigt.
Beim Kauf einer Geschirrspülmaschine sollten folgende Gesichtspunkte beachtet werden.
- Die Spülmaschine sollte ein Schonprogramm haben, das nicht über 60 °C arbeitet.
- Die Spültemperatur in der Maschine muss mit der eingestellten Temperatur am Thermostat übereinstimmen.
- Die Maschine darf beim Wasserwechsel keine schroffen Temperaturunterschiede gestatten.
- Eine genaue Dosierung für Spülmittel und Klarspülmitteln muss gewährleistet sein.
- Die Maschine muss ruhig laufen.
- Der Wasserdruck in der Geschirrspülmaschine darf nicht so hoch sein, dass er Porzellan und Gläser bewegen kann.
- Die vom Hersteller empfohlenen Spülmittel für Glas und Aufglasurdekore müssen erprobt sein.
- Die Einstellkörbe in den Spülmaschinen sollten die günstige Unterbringung auch von Kannen, Schüsseln, Töpfen und ovalen Platten erlauben.
- Die Geschirrspülmaschine muss eine Wasserenthärtungsvorrichtung aufweisen, wenn man an seinem Wohnort hartes Wasser hat.
Sind diese Bedingungen erfüllt, dann wird man sowohl von seinem Porzellan als auch von seinem Glas und Besteck eine dem Wert angemessene Gebrauchsdauer, ohne auffälligen Angriff der Oberflächen und der Dekore, erwarten können. Auch der Wechsel des Spül- oder Klarspülmittels kann entscheidend sein. Es ist unbedingt darauf zu achten, dass das gewählte Mittel dekor- und glasschonend ist.
2  Porzellan und Einfluss von Speisesäuren
Werden Porzellanglasur oder Porzellandekoration durch Speisesäuren (Essig oder Fruchtsäuren usw.) angegriffen? Diese Frage wird sehr häufig gestellt. Da unsere Porzellanglasur eine Feldspatglasur ohne jeden Bleizusatz ist, besteht keine Möglichkeit einer Bleiabgabe oder einer Beschädigung der Glasuroberfläche.
Die einzige Säure, die die Porzellanglasur angreifen kann, ist die Flußsäure, die aber im täglichen Leben überhaupt keine Rolle spielt und nur in bestimmten chemischen Prozessen Verwendung findet. Deshalb sind unsere undekorierten Porzellane, aber auch Unterglasur- bzw. Inglasurdekore vollkommen ungefährdet, denn sie liegen ja unter bzw. in der Glasur und sind von ihr vollkommen umhüllt und geschützt.
Bei den Aufglasurdekoren schützt das sogenannte Bleigesetz (Bundesgesetzblatt Nr. 258 v. 23.12.60). In ihm wird die Verwendung von Bleioxyd als Flußmittel für Glasuren und Dekorationen von Koch- und Essgeschirren geregelt. Demnach ist es verboten, Geschirre herzustellen, die nach 24 Stunden in 4 %iger Essigsäure mehr als 2 Milligramm Blei pro Gefäß an die betreffende Säure abgeben.
Um dieser Gefahr zu begegnen, müssen die Dekore genügend hoch eingebrannt werden und für sie säurebeständige Farben Verwendung finden. Die neuentwickelten Glasurfarben enthalten ebenfalls kein Blei und können deshalb auch kein Blei abgeben. Nur die Glasurfarben für Rot- und Orangetöne enthalten geringe Beimischungen von Cadmium.
Die Abgabewerte liegen aber auch bei diesen weit unter den von der US Food and Drug Administration, FDA festgelegten Grenzwerten, so dass auch hier keine gesundheitliche Gefährdung besteht. Der Verbraucher wird darüber hinaus durch die seit Dezember 1977 gültige DIN Norm 51032 und der mitgeltenden DIN Norm 51031 Teil 1,2,3 vor gesundheitsschädlichen Stoffen geschützt.
Sie bestimmen, dass Bedarfsgegenstände, die mit Lebensmittel in Berührung kommen, kontrolliert werden müssen, ob sie beim Gebrauch gesundheitsbedenkliche Stoffe abgeben. Maßgeblich sind dabei bestimmte Grenzwerte, deren Einhaltung durch zuständige Prüfstellen einer ständigen Kontrolle unterliegen.
3  Die Verwendung von Mikrowellen-Geräten
Man muss heute kein Physiker sein, um dem Begriff der Mikrowelle zu begegnen. Jener Frequenzbereich elektromagnetischer Wellen (im Grenzgebiet zwischen Radio- und Infrarotstrahlung) dient heute ebenso zum Erwärmen, Erhitzen und Garen von Speisen.
Oft gibt es heutzutage in Familien unterschiedliche Essenszeiten. Die Speisen müssen lange warmgehalten werden, aber wie frisch gekocht schmecken. Beim Mikrowellengerät wird die Speise - im mikrowellenfesten Porzellangefäß - angerichtet und bei Bedarf schnell erhitzt.
Das geschieht ohne Geschmacksverluste. Die Mikrowelle verkürzt Kochzeit. Alles was "kühlschrankhart" ist, kann im Nu auf Zimmertemperatur gebracht werden, z. B. wird Butter in 10 Sekunden streichfähig. Besonders gut garen gedünstete, gekochte, geschmorte Lebensmittel (Fisch, Gemüse, Eintöpfe, Auflauf).
Aber auch vorgebräunte Fleischgerichte lassen sich im Mikrowellengerät fertigstellen. Die Mikrowelle ist ideal für die Zubereitung von Baby-, Senioren-, und Diätkost, weil weniger Würze benötigt wird und die Speisen fettarmer angerichtet werden können.
Immer mehr Menschen genießen diese Vorteile der Mikrowelle. Sie benötigen deshalb im zunehmenden Maße mikrowellenfestes Geschirr. Hochwertiges Seltmann Porzellan eignet sich zum Gebrauch im Mikrowellengerät, ohne Schaden zu nehmen.
Ein Tatbestand ist dabei allerdings dringend zu beachten: Mikrowellen greifen Edelmetall an. Es gilt generell: Porzellan mit wertvollen Edelmetalldekoren (Gold, Silber, Platin) nicht in die Mikrowelle!
4  Messer- oder Besteckabrieb
Immer wieder kommen Kunden ins Fachgeschäft, um auf einen ihrer Meinung nach Fehler ihres Porzellans hinzuweisen. Es geht um sogenannte "dunkle Streifen, Kratzer oder Schnitte", die nach einem gewissen Gebrauch auf der Glasur festgestellt werden.
Die weitverbreitete Meinung, es handle sich hierbei um Beschädigungen der Glasur, kann ganz einfach widerlegt werden.
Dieser Messerabrieb lässt sich ganz einfach entfernen: Man nehme eines der heute handelsüblichen, flüssigen und nicht scheuernden Reinigungsmittel, wie sie auch zum Reinigen von Kochflächen benutzt werden, oder das Porzellanreinigungsmittel "etolit" von etol (Infos unter www.etol.de).
5  Hygienisch und Porenfrei
Hygienisch
SELTMANN WEIDEN Porzellan ist absolut dicht gebrannt und nimmt, selbst an den unglasierten Stellen wie den Füßen, keinerlei Flüssigkeiten auf. Dies ist ein entscheidendes Plus für die Hygiene.
Porenfrei
Die absolut glatte Oberfläche unserer Glasur zeigt keine Poren, in denen sich Schmutz oder gesundheitsschädlichen Bakterien festsetzen könnten. Ein weiteres wichtiges Plus sowohl in Sachen Hygiene als auch im Hinblick auf die Gesundheit.
Hygienisch
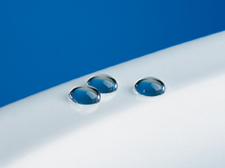
SELTMANN WEIDEN Porzellan ist absolut dicht gebrannt und nimmt, selbst an den unglasierten Stellen wie den Füßen, keinerlei Flüssigkeiten auf. Dies ist ein entscheidendes Plus für die Hygiene.
Porenfrei
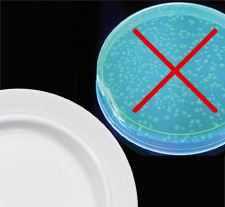
Die absolut glatte Oberfläche unserer Glasur zeigt keine Poren, in denen sich Schmutz oder gesundheitsschädlichen Bakterien festsetzen könnten. Ein weiteres wichtiges Plus sowohl in Sachen Hygiene als auch im Hinblick auf die Gesundheit.
6  Unsere Produkte sind Salamanderfest
Seltmann Hartporzellan ist bestens für den Einsatz in einem "Salamander" geeignet. Im Salamander werden Teller und Platten in sehr kurzer Zeit vorgewärmt, um die Gerichte lange auf die für den Verzehr optimale Temperatur zu halten.
Der Salamander dient auch zum Überbacken und Gratinieren von Gerichten. In allen Anwendungsfällen ist Hartporzellan der optimale Werkstoff, da es der sehr raschen Erhitzung standhält und ein sehr hohes Wärmespeichervermögen besitzt.
7  Forschungsprojekte
Verbesserung der Energiebilanz mit LfU-München Verbesserung der Energiebilanz mit dem LfU1998 arbeitete Seltmann stellvertretend für die Porzellanindustrie eng mit dem Landesamt für Umweltschutz (LfU) zusammen, um für das Werk Erbendorf Konzepte für die Energieeinsparung zu erarbeiten. Das LfU hatte das Werk Erbendorf gewählt, weil dieser Betrieb in Bayern der modernste seiner Art ist. Die Rauchgase aus dem Porzellanbrand werden in großzügig bemessenen Filteranlagen gereinigt. Die vom Gesetzgeber geforderten Grenzwerte werden damit nicht nur erfüllt, sondern unterschritten. Die Prozesswärme des Porzellanbrandes wird weitestgehend zurückgewonnen, und für Raumheizung und Warmwasseraufbereitung genutzt.
Im Werk Erbendorf wurde in modernste Brennöfen investiert, die neben ihrem sehr hohen Wirkungsgrad (weniger Abwärmeverluste) auch schwankenden Kapazitätsanforderungen angeglichen werden können. Im Zeitraum 1998 und 1999 wurden weitere zwei Millionen DM in die Einsparung von Energie investiert.
8  Die Erfinder des Porzellans
Bereits seit der Hochblüte der west-chinesischen Kulturen (1122 bis 770 v.Chr.) ist Porzellan als Produkt der Chinesen bekannt. Porzellan wurde in China nicht erfunden, sondern gilt als Ergebnis eines langen Entwicklungsprozesses. Auf mühevollen Wegen gelangten Porzellanteile ab dem 13. Jahrhundert durch Kaufleute, Forscher und Weltreisende wie Marco Polo nach Europa.
Erst seit dem 17. Jahrhundert wurde Porzellan hauptsächlich über Holland importiert. Die Herstellung des damals sehr kostbaren Materials blieb jedoch das Geheimnis der Chinesen – es musste in Europa neu erfunden werden. Mit dem deutschen Alchimisten und Apotheker-Gehilfen Johann Friedrich Böttger (1682 – 1719) wird die Erfindung des Porzellans verbunden.
Anfang des 18. Jahrhunderts begannen gemeinsame Forschungen von Johann Friedrich Böttger, Ehrenfried Walther von Tschirnhausen (Tschirnhaus), dem Freiberger Bergrat Gottfried Pabst von Ohain und weiteren fachkundigen Berg- und Hüttenleuten im Auftrag Augusts des Starken zur Entschlüsselung des Herstellungsgeheimnisses von Porzellan.
Die Arbeiten führten zum Erfolg. 1708/1709 gelang dem Team unter Leitung von Johann Friederich Böttger erstmals die Herstellung des weißen Hartporzellans („Weißes Gold“). Mit königlichem Dekret vom 23. Januar 1710 wurde die erste europäische Porzellanmanufaktur von August dem Starken in Dresden gegründet und im März desselben Jahres nach Meißen auf die Albrechtsburg verlegt.
Johann Friedrich Böttger wurde als Leiter der Manufaktur eingesetzt.
9  Geschichte der Porzellanindustrie
Das Mediciporzellan, das französische Frittenporzellan, das Réamurporzellan, das Fayenceporzellan und viele andere waren keine Porzellane, da sie nicht alle Eigenschaften besaßen. Daher ist es sehr schwer festzustellen, welche “Porzellanfabriken-manufakturen” wirklich das Porzellan herstellten. Als die italienischen Majoliken außer Mode kamen, trat die Fayenceware mit weißer Glasur und blauer Farbe an ihre Stelle.
Das auch die im 19. Jahrhundert entstandenen Betriebe der Oberpfalz gerne Fayenceporzellan als Porzellan verkauften, war aufgrund von Absatzschwierigkeiten, Kapitalmangel /-mobilität und weiterer Faktoren nicht ausgeschlossen.
Die Firmenbezeichnung Porzellanfabrik wurde nur allzu gern der Bezeichnung Fayence vorgezogen, da die Porzellanherstellung in der Bevölkerung ein hohes Ansehen genoß.
Vorgeschichte
Der Wunsch, Porzellan zu besitzen, wurde ausgelöst durch Schalen, Vasen und Dosen, die Marko Polo im 13. Jahrhundert von seinen Reisen aus China mitbrachte. Die Geschichte des europäischen Porzellans beginnt mit der Entdeckung der Herstellungsmethode durch Ehrenfried Walther von Tschirnhaus (1651-1708) und Johann Friedrich Böttger. Von Tschirnhaus gelang es, nach jahrelangen Versuchen in seinem Schmelztiegel das erste Stück weißes Hartporzellan herzustellen. Vorausgegangen waren die Bemühungen Böttgers auf der Albrechtsburg bei Meißen auf Geheiß August des Starken, dem Kurfürst von Sachsen und König von Polen, Gold herzustellen.
Statt Gold zu erfinden, schlug die Geburtsstunde des Porzellans. Tschirnhaus entwickelte hierfür einige Brennspiegel, die zur Erreichung der hohen Temperaturen dienten. Im Oktober 1708 fertigte er noch einen Porzellanbecher. Nach von Tschirnhaus Tod (11.10.1708) führte Böttger die Porzellanforschung fort. 1709 gelang ihm die Herstellung eines roten Steinzeugs, das nach ihm "Böttger-Steinzeug" genannt wurde.
Entwicklung
Das neue Porzellan, das Hartporzellan, erfährt heute ständige Verbesserungen hinsichtlich der Feuerfestigkeit (für GV-Kochstellen), Kantenbruchfestigkeit, Oberflächenhärte, Stapelfähigkeit und Spülmaschinenfestigkeit.
Erst dadurch ist der Einsatz im Systemgeschirrbereich und Großküchen möglich. Es entstehen die Produktgruppen “Systemgeschirr” und “GV-Porzellan”. Die Entwicklung der Porzellanindustrie bis zum Ende des 19. Jahrhunderts vollzog sich in drei Schritten.
Betrachtet man diese unter Berücksichtigung der Erzeugnisse, so wurden in der ersten Periode vornehmlich “Luxusporzellane”, Luxusartikel und handgemalte Figuren hergestellt.
Einfache Formen und relativ dicker Scherben kennzeichneten in der zweiten Periode die Einführung der “Gebrauchsgeschirre”.
Die Erhöhung der Qualität in der dritten Periode, die sich durch einen feinen Scherben auszeichnete, ließ das “feine Tafelgeschirr” entstehen.
Heute verwendet man unter letzerem ebenfalls die Bezeichnung Gebrauchsgeschirr.
Das Porzellan und die Oberpfalz
Wegen der komplizierten und kostspieligen Produktion konnte das Porzellan nicht in größeren Mengen fabriziert werden. Die Herstellung lag ausschließlich in den Händen der regierenden Fürsten und war an sie gebunden: Zum einen diente der Betrieb, der im Schloss integriert war, als Einnahmequelle, zum anderen sollte die Tischkultur ihn profilieren.
Die Rohstoffe Quarz und Feldspat waren leicht zu erhalten, doch das Kaolin war zunächst selten und kostbar. In der zweiten (merkantilistische Periode) war für die Gründung eines Unternehmens in erster Linie die Standortlehre ausschlaggebend. Der Betrieb konnte nun auch außerhalb der Schlösser liegen.
Die Porzellanbetriebe waren in der Regel dort angesiedelt, wo Brennmaterial und Arbeitskräfte vorhanden waren. Diese beiden Faktoren wirkten sich stärker in der Standortwahl aus als die verhältnismäßig hochwertigen Rohstoffe.
Einerseits wurde die Wahl der Abnehmer nicht mehr vorgeschrieben, andererseits mußte der Unternehmer auf die finanzielle Unterstützung des Fürsten verzichten. Die dritte Periode ließ nach dem Krieg (1870) die meisten Fabriken dort entstehen, wo bereits die Porzellanindustrie ansässig war oder die Verkehrsanbindung es ermöglichte.
Die Entwicklung der Porzellanindustrie machte ab jetzt ihre größten Fortschritte.
Der erste Betrieb
Ihre größte Verbreitung hatte die Porzellanindustrie hinsichtlich der Anzahl der Betriebe in Thüringen, gefolgt von Schlesien, Saargemünd und Oberfranken.
Wie in der gesamten Oberpfalz befanden sich in Regensburg nur wenige Betriebe dieser Branche. Verschiedene Umstände führten zur Einführung der Porzellanherstellung in der Oberpfalz: Der nördliche Teil der Oberpfalz liegt zwischen den Rohstoffvorkommen in Böhmen und den ersten Manufakturen in Thüringen.
Es war damit nur noch eine Frage der Zeit (und des Kapitals), bis sich die ersten Porzelliner in dieser Region niederließen. Dass im 18. Jahrhundert keine Betriebe entstanden waren, ist damit zu begründen, dass zum einen die Zunftfesseln der alten Reichstadt erst zu Beginn des 19. Jahrhunderts abgestreift wurden und zum anderen es am Kapital mangelte. Der Unternehmer Koch gründete im Jahre 1803 den ersten oberpfälzischen Porzellanbetrieb in Regensburg, der später unter dem Namen Schwerdtner bekannt wurde. Das finanzielle Problem konnte erst nach dem Einzug des Mainzer Fürsten C.Th. von Dalberg gelöst werden, da dieser dem Projekt sehr wohlwollend und finanzkräftig gegenüberstand. Eine Unternehmensgründung außerhalb Regensburgs war in der Oberpfalz also unmöglich.
Die Standortfrage
Weitere Gründe für die Niederlassung der Porzellanherstellung war der Reichtum an Brennstoffen, die gefundenen Kaolinlager in Amberg, Pressath, Kemnath und Mitterteich sowie die billigen Arbeitskräfte. Die ansässige Glasindustrie führte die durch ähnliche Handgriffe geschulten Arbeitskräfte der Porzellanindustrie zu.
Gerade für die Porzellanindustrie war es wichtig, dass die Manufaktur nie dem Zunftzwang unterworfen war. (Dass die Gründung der Regensburger Porzellanfabrik in dem Zunftwesen eine Behinderung gesehen haben soll, mag daran liegen, dass dieser Betrieb nicht als Manufaktur anerkannt wurde, weil sich doch die Wohnung und die Betriebsstätte in einem eher bescheidenen Anwesen befanden).
Die Porzellanindustrie glich einem modernen Gewerbezweig, in dem das Handwerk nie festen Fuß fassen konnte. Allerdings war man von der Massenproduktion noch weit entfernt.
Erste Absatzschwierigkeiten
Das Hauptabsatzgebiet der Porzellanindustrie um 1806 war der Orient, während die lokale Nachfrage mit Fayence- und Steingutprodukten befriedigt wurde. Am Porzellan kann man verfolgen, wie aus einem exklusiven Produkt für wenige durch die industrielle Entwicklung, duch allmähliche Verbilligung der Produktion die Erzeugnisse zu einem allgemeinen Bedürfnis wurden.
Sobald die Produktion aufgenommen wurde, zeigte sich noch bis zur Jahrhundertmitte, dass die Nachfrage fehlte. Ursachen waren neben der Neuheit des Fabrikates, die anfänglich ziemlich hohen Preise, die geringe Kaufkraft weiter Schichten sowie deren Bedürfnislosigkeit.
Die Regensburger Porzellan- und Steingutfabrik unter der Leitung von Koch musste nach 7 Jahren nach der Betriebsaufnahme die Produktion auf Steingut umstellen, da dieser Bereich einen ungeahnten Aufschwung erlebte.
Die Kombination aus Porzellan- und Steingutfabrik, die man auch leicht an Hand der Firmennamen erkennt, ermöglichte es dem Unternehmen einen breiteren Kundenkreis anzusprechen. Schnell wurden die Vorteile des Porzellans gegenüber des Tonscherben erkannt:
Das Aussehen und die Haltbarkeit des Porzellan lösten ab den 50er Jahren eine erhöhte Nachfrage nun auch bei der breiten Bevölkerung aus. Sie schaffte die Grundlage für Gründung neuer Unternehmen.
Die neue Energiequelle
Die Wälder gaben längst nicht mehr soviel Holz als die Fabriken mit ihren Öfen brauchen würden. Gleich zu Beginn machten sich die Fabriken deshalb vom Wasser (Wassermangel in den Sommermonaten) und vom Holz der Wälder unabhängig.
Die langflammige Braunkohle wurde die Betriebsstoffgrundlage der Porzellanindustrie. Um diese Zeit entstand die Steingut- und Porzellanfabrik Heinrich Waffler, die vom Ende der 1850er Jahre bis um die Jahrhundertwende existierte.
Gleichzeitig hatte (ab 1856) die Gewinnung der Porzellanerde und die Schlemme eine außerordentliche Ausdehnung erfahren. In der Gegend zwischen Amberg, Schnaittenbach und Freihung wurden jährlich 10.000 Tonnen teils als Rohstoff, teils als Fertigprodukt aus den Betrieben in Marberg und Hirschau versendet.
Eine Ausweitung der verarbeitenden Betriebe wäre, wie auch der Rest der Porzellanindustrie fordert, nur dur
10  Grundlagen der Herstellung
Die Herstellung von Hartporzellan hat eine der höchsten Fertigungstiefen aller industriell gefertigten Produkte: vom Rohstoff bis zum Fertigprodukt werden alle Fertigungsschritte in einem Werk vollzogen..
Unsere Rohstoffe
Die Hauptbestandteile unserer Porzellanmasse sind: Kaolin, Ton, Quarz, Feldspat, Dolomit, Kalkspat, Kreide. Der hohe Quarzgehalt in unserer Glasur und Masse ergibt in Verbindung mit den anderen Rohstoffen hohe Festigkeitswerte und Verschleißbeständigkeit.
Für unsere Hartporzellanherstellung werden nur natürliche Rohstoffe für Masse und Glasur verwendet. Dabei werden die Mineralien, die meist im Tagebau gewonnen werden, zuerst beim Rohstofflieferanten aufbereitet. Die notwendigen Verfahrensschritte sind dort in der Regel Zerkleinern, Begleitmineralien abtrennen, Waschen, Sieben und Trocknen. Dabei kann das Verfahren sehr komplex sein, um z. B. färbende Begleitmineralien (z.B. Eisenverbindungen), die im Porzellan nicht erwünscht sind, abzutrennen. Für unser Qualitätsporzellan können nur Rohstoffe eingesetzt werden, die frei von Begleitmineralien sind, und die in ihrer chemischen und mineralogischen Zusammensetzung von Lieferung zu Lieferung gleich sind.
Die Aufbereitung unserer Hartporzellanmassen
Die Rohstoffe bedürfen einer intensiven Vermahlung und Vermischung. Dazu werden die sogenannten 'Hartstoffe' (Quarz, Feldspat, Dolomit, Kalkspat, Kreide) in Trommelmühlen, zusammen mit Wasser und Mahlkörpern, aufgemahlen. Die größten Mühlen fassen mehrere Tonnen Rohstoffe, und der Mahlprozess für die Glasur dauert mehrere Tage. Nach beendeter Mahlung werden die plastischen Rohstoffe (Kaolin und Ton) zu den Hartstoffen zugegeben, und die gesamte Mischung (der 'Porzellanversatz') intensivst vermischt. Danach wird die Rohstoffsuspension abgesiebt und über Magnete geleitet, um auch die kleinste Verunreinigung zurückzuhalten. Die Suspension wird dann einer Filtration in sogenannten 'Kammerfilterpressen' unterzogen.
Hier wird der größte Teil des Prozesswassers abgetrennt, und es resultieren Massekuchen mit einem Wassergehalt zwischen 18% und 22%. Diese Massekuchen sind das Vorprodukt für die beiden Formgebungsverfahren 'Drehen' (z.B. Teller, Tassen, Salatschüsseln) und 'Gießen' (z.B. Zuckerdosen, Kaffee- oder Teekannen, Saucieren). Für das 'Drehverfahren' wird der Massekuchen in einer sogenannten 'Vakuumstrangpresse' zu einem Massestrang verarbeitet, wobei die Porzellanmasse gleichzeitig durch Vakuum von eingeschlossener Luft befreit wird. Damit erzielt man eine sehr bildsame Masse, die auch feinste Details des Modells wiedergeben kann. Für die Formgebung durch 'Gießen' werden die Massekuchen mit Wasser und einem sogenannten 'Verflüssiger' zu einer Suspension aufbereitet, deren Konsistenz der von Sahne sehr ähnlich ist.
Formgebung
Bei der Formgebung der Porzellanartikel unterscheidet man im Wesentlichen drei Verfahren: Das Drehen (Formen) der plastischen (feuchten) Porzellanmasse, das Pressen (Verdichten) einer pulverförmiger Masse, das Giessen einer flüssigen Masse, das auch durch Anwendung von Druck (Druckguß) beschleunigt werden kann.
Die Flachgeschirrdreherei
Beim Formen von Tellern wird eine Scheibe der Porzellanmasse zwischen einer Gipsform und einer heheizten, rotierenden Stahlschablone ausgeformt. Dabei wird die Ansichtsseite des Tellers durch die Gipsform bestimmt, während die Stahlschablone die Rückseite des Tellers ausformt. Nach diesem Vorgang wird die Gipsform zusammen mit dem Artikel ca. 30 Minuten bei 60°C getrocknet. Danach kann der Teller von der Gipsform abgehoben werden. Die leere Gipsform wird dem Formgebungsvorgang wieder zugeführt, und dabei getrocknet, um wieder Feuchtigkeit aus der Porzellanmasse aufnehmen zu können.
Die Gipsformen haben allerdings eine begrenzte Lebensdauer. Bei Tellern, die mit einem Relief versehen sind, genügt die Oberfläche der Gipsform bereits nach 50 Zyklen nicht mehr den Anforderungen des Qualitätsporzellans.
Bei Tellern, die nicht mit einem Relief versehen sind, kann die Gipsform ca. 120 mal überformt werden. Der Artikel selbst wird dann weiter intensiv getrocknet, was die Voraussetzung für den nun folgenden ersten Brand, den sogenannten Gühbrand ist.
Die Flachgeschirrpresserei
Die Kosten für die Herstellung einer Pressform sind sehr hoch. Aufwändige Konstruktionen erfordern vom CAD-System beträchtliche Leistungen. Drehformen sind im Gegensatz zu Presswerkzeugen erheblich schneller herzustellen, haben allerdings nur eine begrenzte Lebensdauer und müssen daher ständig ersetzt werden.
Beim Pressen wird die keramische Masse als Pulver zwischen einem Ober- und Unterstempel mit einem Druck von ca 300bar verdichtet. Auf diese Weise hergestellte Artikel müssen i.d. Regel vor dem ersten Brand (Glühbrand) nicht getrocknet werden.
Außerdem müssen im Gegensatz zum Drehverfahren keine Gipsformen erzeugt werden. Mit diesem Verfahren ist die Herstellung von sehr maßgenauen Tellern, mit breiten, flachen Fahnen möglich. Die Wiedergabe auch von feinen Details im Reliefs bleibt über die gesamte Lebensdauer der Pressform konstant.
Die Becherdreherei
Jetzt wird noch der Henkel, der im Gießverfahren (siehe dort) hergestellt wird, in Handarbeit an den Körper angarniert. Bevor die Tasse in den ersten Brand gehen kann, muss sie noch intensiv getrocknet werden.
Die in der Masseaufbereitung hergestellten Massezylinder ('Hubel') werden in der Maschine zur Herstellung von Tassen nochmals zu dünneren Massesträngen gezogen. Von diesen werden Massestücken abgeschnitten, die dann mit einer Stahlschablone (Innenkontur) und einer Gipsform (Außenkontur) zu einem Tasse ausgeformt werden. Danach wird die Form zusammen mit dem Artikel ca. 7 Minuten bei 60°C getrocknet. Die Tasse (noch ohne Henkel) kann jetzt der Gipsform entnommen werden. Die leere Form wird nach einer Rücktrocknung wieder dem Formgebungsvorgang zugeführt. Der Tassenkörper bedarf noch einem Verrunden des Mundrandes. All diese Vorgänge sind automatisiert, weshalb die Maschine die Bezeichnung 'Tassentaktstrasse' trägt.
Das Druckgießverfahren
Beim Druckgießen wird nicht wie beim Gießen (Hohlgussteile wie Kannen) oder Drehen (Teller oder Tassen) der Werkstoff Gips als Entwässerungsform eingesetzt, sondern ein poröser Kunststoff. Dieses Verfahren wird für 'Vollgussteile' wie ovale und rechteckige Platten oder Auflaufformen eingesetzt. Der Druck, mit dem das "flüssige Porzellan" (Schlicker) zwischen die Kunststoffhälften gepresst wird, beträgt ca. 30 bar. Das Wasser des Schlickers wird durch die Poren des Kunststoffes herausgepresst, es findet eine Filtration statt, die zwischen 30 Sekunden und mehreren Minuten dauert. Danach kann der Artikel aus der Form genommen werden. Es schließt sich das verputzen der Formnaht (Grat) und das Trocknen des Artikels an. Die Vorteile der Kunststoffform gegenüber der Gipsform sind eine weit höhere Lebensdauer, eine höhere Maßhaltigkeit des erzeugten Artikels und detailgetreue Wiedergabe von Reliefs über die gesamte Lebensdauer der Form.
Die Gießerei
Für das Gießverfahren werden die Massekuchen aus der Masseaufbereitung (siehe dort) mit Wasser und Verflüssigern zu einem Schlicker aufbereitet. Dieser wird in eine Gipsform gegossen, die mindestens aus zwei Teilen besteht. Der Gips saugt das Wasser aus dem Porzellanschlicker auf, und es baut sich eine relativ feste Schicht Porzellanmasse an der Gipsform auf.
Dieser Prozess des kontinuierlichen Aufbaus des Artikels dauert einige Minuten. Wenn die gewünschte Wandstärke des Teiles erreicht ist, wird der überschüssige Schlicker ausgegossen, und dem Prozess wieder zugeführt. Die Form mit dem an der Wandung aufgebauten Artikel wird mit Warmluft beaufschlagt um eine Verfestigung des Artikels zu erzielen. Danach kann die Form geöffnet, und der Artikel entnommen werden.
Nach endgültiger Trocknung wird der Artikel in Handarbeit von den Formnähten (Grat) befreit. Die leere Gipsform wird nach einer Trocknung wieder einem neuen Gießprozess zugeführt.
Die Trocknung
Die Beheizung der Trockner erfolgt meist mit Abwärme aus den Brennöfen, oder mit Brennern, die mit Erdgas gespeist werden.
Nach der Formgebung müssen die Artikel getrocknet werden, um danach den ersten Brand, den Glühbrand, zu durchlaufen. In den Durchlauf- oder Kammertrocknern werden die Teile mit warmer Luft von 40°C bis 120°C beaufschlagt. Die Trockenzeit beträgt mehrere Stunden bei Geschirrteilen, und kann mehrere Tage bei Porzellanfiguren erfordern.
Der erste Brand: Der Glühbrand
Nach dem Brand wird die Masse durch das Eintauchen in Wasser nicht mehr weich, ist etwas verfestigt, und besitzt eine hohe Porosität. Diese Merkmale sind